In 2025, acronyms move fast—especially in industries where precision, quality, and communication matter. One of those acronyms, DPMO, stands out. You’ve probably seen it in quality control reports, Six Sigma manuals, or even in casual conversations online. But what exactly does DPMO mean, and why should you care? In this complete guide, you’ll get the best DPMO meaning & usage—broken down simply and explained with examples, use cases, and alternatives.
Whether you’re a professional in manufacturing or just stumbled upon this term in a chat, this guide will help you understand DPMO in all its forms and use it with confidence.
What Does DPMO Mean?
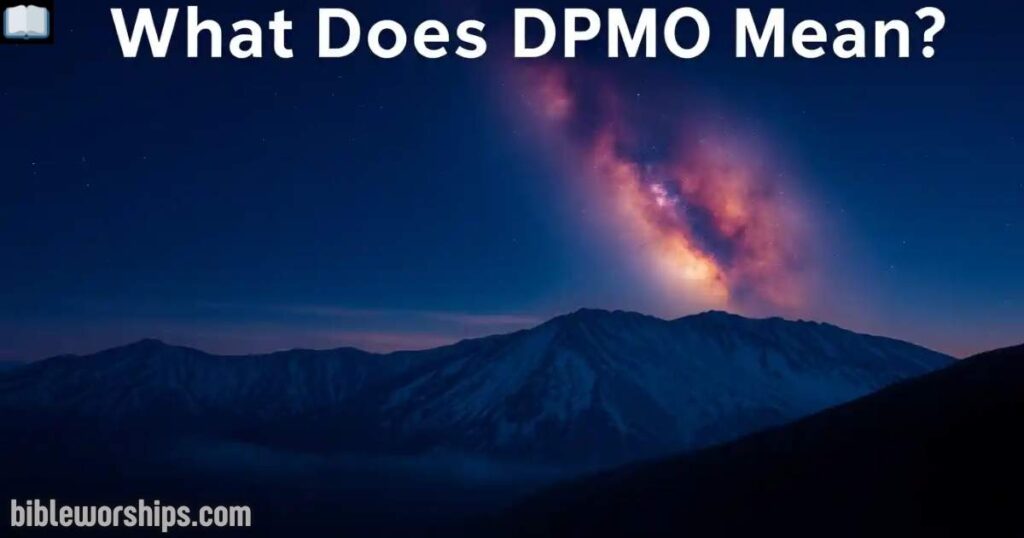
DPMO stands for Defects Per Million Opportunities. It’s a quality management metric used to measure how many defects occur in a process out of one million possible opportunities. It helps businesses evaluate their performance, especially in manufacturing or services where precision is critical.
For example, if you’re producing smartphones and each phone has 10 opportunities for defects (screen, buttons, battery, etc.), and you produce 10,000 phones, that’s 100,000 total opportunities. If 100 defects are found, the DPMO = (100 ÷ 100,000) × 1,000,000 = 1,000 DPMO. This means you have 1,000 defects per million opportunities—a metric that can guide process improvement.
Origins of DPMO
DPMO emerged from the Six Sigma methodology, a system designed to improve processes by identifying and removing causes of defects. Six Sigma became widely popular in the 1990s, driven by companies like Motorola and GE, who used it to save billions by refining their production lines.
Since then, DPMO has become a go-to metric for anyone serious about quality control. Unlike simpler metrics like “defect rate,” DPMO accounts for complexity. It doesn’t just ask how many items are defective, but how many chances there were for something to go wrong—making it far more precise.
When to Use DPMO in Professional Settings
DPMO shines in manufacturing, engineering, healthcare, and logistics—anywhere that accuracy and consistency matter. Managers use it to benchmark quality across time, teams, or processes. For example, if Line A has a DPMO of 300 and Line B has 1,200, you know exactly where to look for improvements.
It’s also valuable in compliance reporting. Regulatory industries—such as pharmaceuticals or aviation—use DPMO to show they meet strict safety standards. A consistently low DPMO score signals a well-controlled, high-quality operation.
Using DPMO Casually (Texting and Social Media)
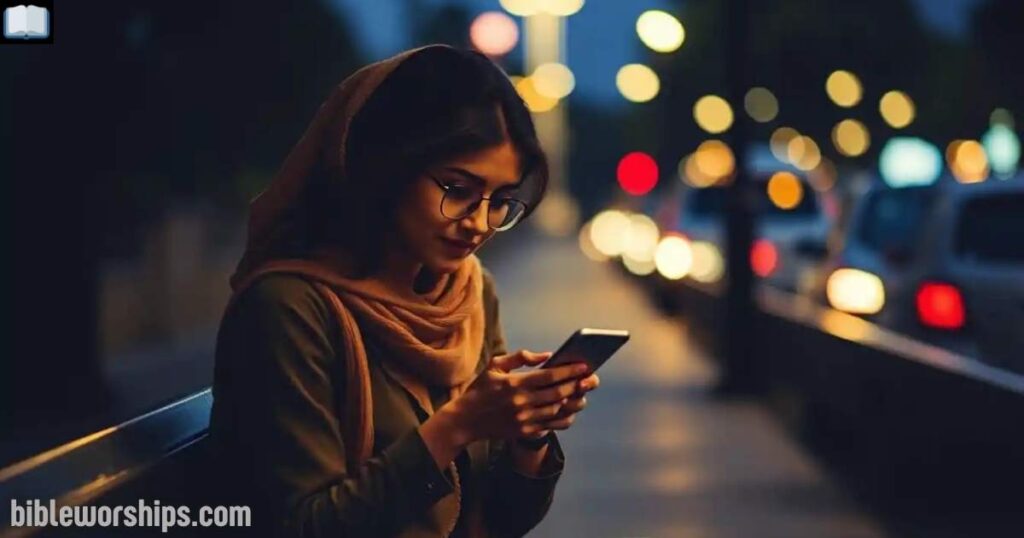
Surprisingly, DPMO has also found its way into casual language, especially among Gen Z and meme culture. In texting or online chats, some interpret DPMO as “Don’t Piss Me Off”—a bold, slightly edgy way to warn someone not to cross a line.
In this context, the tone is playful or sarcastic. For example:
“I’ve had enough work for today, DPMO 😤”
This slang usage is far less common than the professional one but has gained some traction in informal chats, especially on Twitter, TikTok, and Instagram captions.
Alternatives to DPMO (Professional Context)
If DPMO doesn’t fit your reporting needs, other metrics can offer similar insights. Here are some alternatives:
- PPM (Parts Per Million): Simpler than DPMO but doesn’t account for multiple defect opportunities per unit.
- DPU (Defects Per Unit): Tracks how many defects occur per item but lacks the granularity of DPMO.
- Sigma Level: Expresses quality in statistical terms (e.g., 3σ, 6σ), often converted from DPMO.
Each of these metrics serves a different layer of insight. But when you need to factor in complexity, DPMO usually gives you the clearest view.
Alternatives to DPMO (Casual Context)
In casual speech, if “DPMO” as “Don’t Piss Me Off” feels too harsh, here are softer or funnier alternatives:
- IDC (I Don’t Care): A laid-back way to disengage from the convo.
- SMH (Shaking My Head): Shows disappointment or disbelief.
- BRB (Be Right Back): A neutral pause instead of escalating.
You can also use emojis to soften the tone:
“DPMO 😂” vs. “DPMO 😡” — see the difference?
Understanding tone and timing is key in casual messaging. Acronyms can build rapport—or cause confusion—depending on how you use them.
How to Choose the Best Alternative
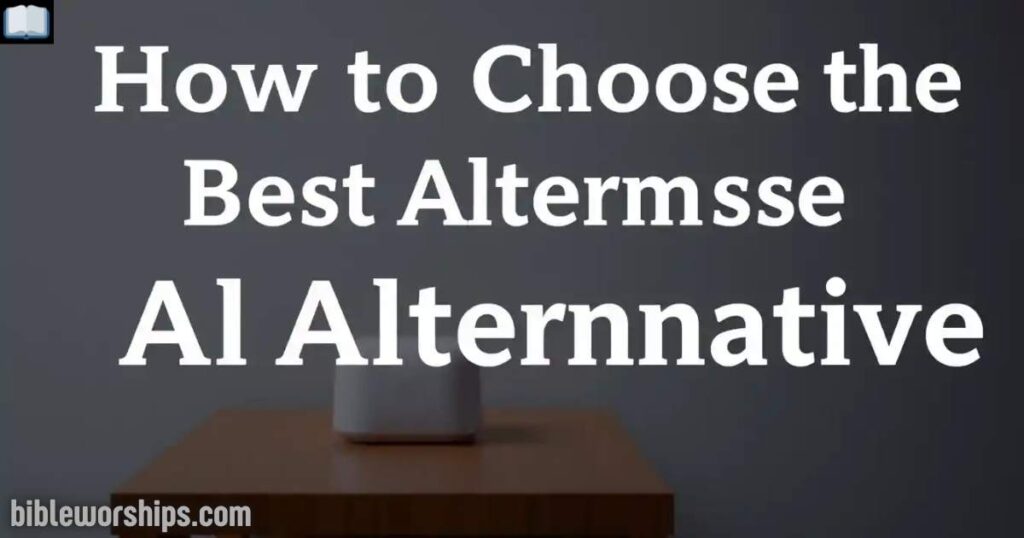
Context is everything. In professional environments, DPMO is a reliable metric—but only when your process involves multiple possible defects per unit. If not, PPM or DPU might make more sense. Ask yourself:
- What’s the audience? (Manager, regulator, peer)
- What are you tracking? (Units, steps, or defects?)
- How complex is the process? (Single vs. multiple defect types)
In texting or social media, consider how the acronym might be interpreted. Humor and tone matter more than precision here. Make sure your use fits the flow of the conversation, not just the acronym itself.
Texting Examples of DPMO and Alternatives
To make it more practical, here’s a table with sample texts using DPMO and its alternatives:
Context | Acronym Used | Sample Message | Meaning |
Casual Chat | DPMO | “If my pizza’s late again, DPMO 😂” | Don’t Piss Me Off (playful) |
Social Media | SMH | “Still no raise after 2 years… SMH.” | Disbelief/disappointment |
Work Email | DPMO | “Line 2 shows a DPMO of 800—needs immediate check.” | Quality metric |
Slack Message | PPM | “Let’s use PPM instead of DPMO for simplicity.” | Alternate metric (work context) |
Texting | IDC | “IDC what they think. I’m done.” | I Don’t Care (dismissive tone) |
Why DPMO Still Matters in 2025 (And Beyond)
With automation, AI, and real-time monitoring becoming the norm in industries, DPMO remains a timeless metric. Why? Because even the smartest systems can’t eliminate the need for human decision-making. DPMO gives professionals a clear, scalable way to track quality, regardless of the tech stack or tools being used.
As more companies adopt lean practices and digital quality control platforms, DPMO helps maintain a standard language across teams, locations, and even countries. Whether you’re a Six Sigma Black Belt or just learning quality basics, understanding DPMO puts you ahead of the curve.
Tips for Using DPMO Effectively in Your Work
If you’re planning to use DPMO in a professional setting, here are a few practical ways to make the most of it:
- Define “Opportunity” Clearly
Not every step in a process is a valid opportunity for a defect. Clarify what counts and stick to it for consistent results. - Track DPMO Over Time
A single DPMO score isn’t enough. Monitor changes week-to-week or quarter-to-quarter to see trends and areas of improvement. - Combine With Root Cause Analysis
DPMO tells you how much is going wrong—not why. Pair it with root cause analysis to solve problems more effectively. - Use Visual Aids
Graphs, control charts, and dashboards can make DPMO data more accessible to stakeholders who aren’t deep in quality control. - Don’t Ignore Small Wins
Even a slight drop in DPMO can signal important process improvements. Celebrate progress and keep momentum going.
Final Thoughts
In both professional and casual settings, DPMO is more than just an acronym—it’s a reflection of precision, efficiency, and even attitude. In business, it gives you the numbers you need to improve. In texts or tweets, it expresses emotion with punchy flair. Understanding its double life—and using it appropriately—puts you in control of both your communication and your outcomes.
So the next time you hear “DPMO,” don’t just nod and move on. Think about what it really means in that context—because whether you’re presenting at a board meeting or joking with a friend, the right usage makes all the difference.
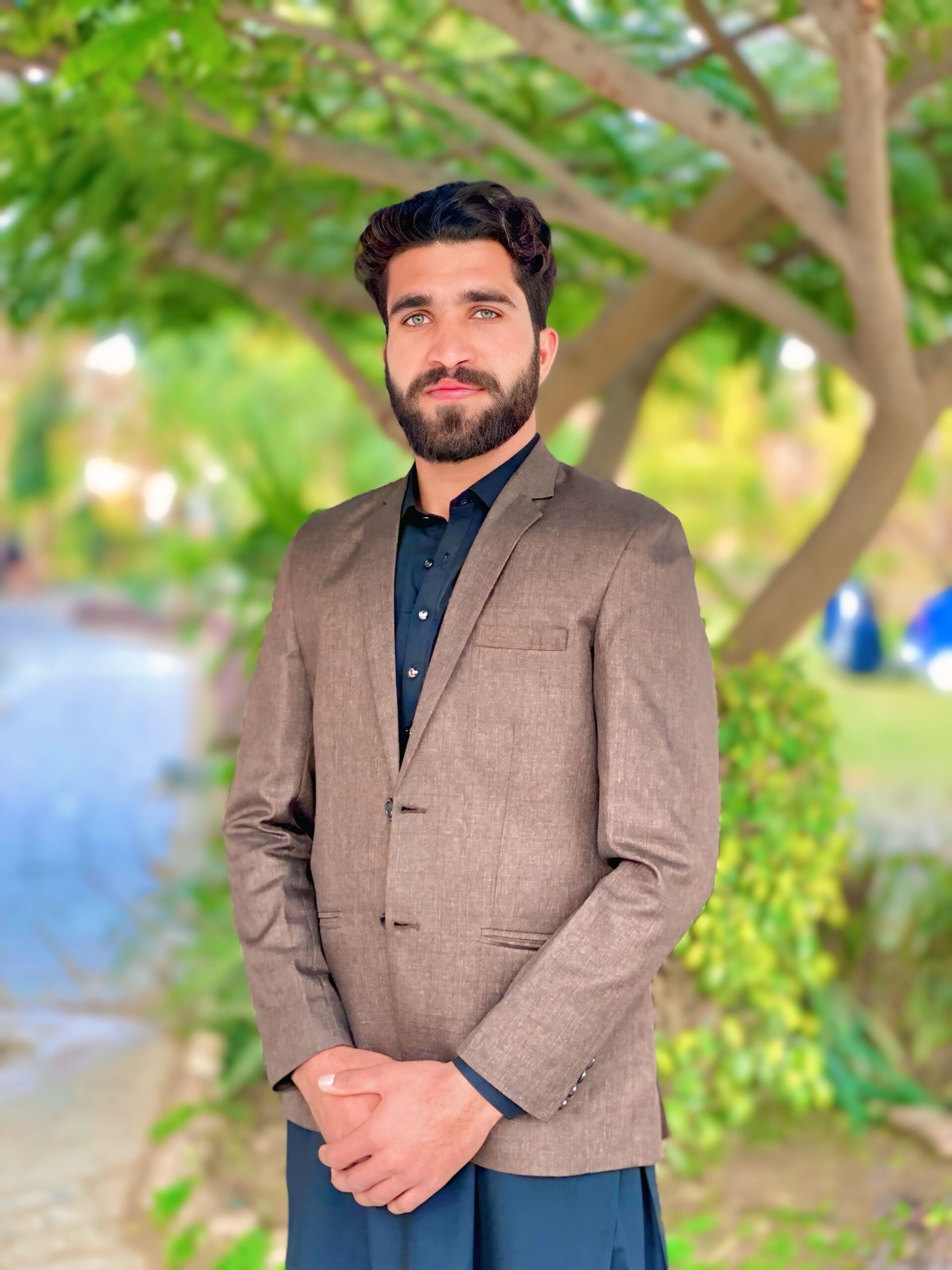
My name is Razzaq, and I have been writing about Bible verses and prayers for a long time. My deep understanding of these topics allows me to create high-quality content. The information I provide is always 100% accurate, ensuring that readers receive reliable and valuable insights.